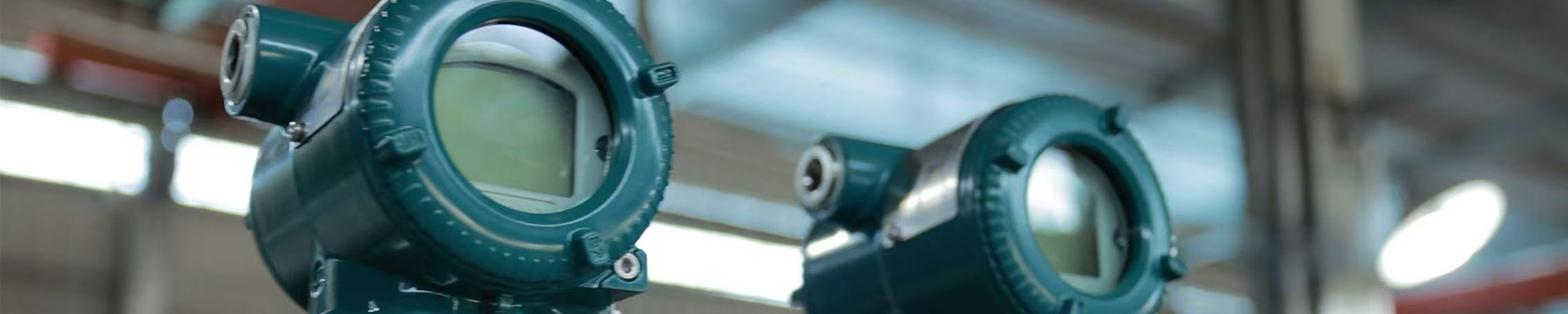
Understanding Cryogenic Pump Skids: Components, Working Principles, and Applications
2025-03-26 22:07In the realm of industrial gas processing and energy management, cryogenic pump skids play a pivotal role in transforming stored liquids into high-pressure gases for diverse applications. These systems are engineered to enhance efficiency and safety in handling cryogenic fluids, such as liquefied natural gas (LNG) or other low-temperature liquids. A typical cryogenic pump skid is equipped with five critical pipe interfaces: an inlet pipe, outlet pipe, low-pressure vent pipe, high-pressure vent pipe, and return pipe. This article delves into the components, operational mechanisms, and practical considerations of cryogenic pump skids, offering insights for engineers, plant managers, and industry professionals seeking optimized solutions for gas pressure management.
Core Components and Functional Design
The cryogenic pump skid’s design revolves around its five specialized pipe interfaces, each serving a distinct purpose. The inlet pipe connects the skid to the storage tank, allowing cryogenic liquid to flow into the system. Once inside, the cryogenic pump pressurizes the liquid, converting it into a high-pressure gas ready for distribution or use. The outlet pipe then channels this pressurized gas to its intended application, such as fueling stations, industrial burners, or power generation units.
Safety and pressure regulation are critical, which is where the low-pressure vent pipe and high-pressure vent pipe come into play. These vents prevent over-pressurization by safely releasing excess gas when system pressures exceed predefined thresholds. Finally, the return pipe facilitates the controlled return of gas to the storage tank or venting system during startup or shutdown procedures, ensuring stable operations. Together, these components create a closed-loop system that prioritizes efficiency, safety, and reliability.
Operational Workflow and Safety Protocols
The operation of a cryogenic pump skid begins with the proper sequencing of valves and systems. Before activating the pump, operators must first open the return pipe valve to establish a controlled pathway for gas return. This step is crucial to prevent pressure surges that could damage the pump or downstream equipment. Once the return line is primed, the cryogenic pump is started, drawing liquid from the storage tank and pressurizing it for distribution.
During operation, the high-pressure vent pipe monitors and releases gas if the outlet pressure exceeds safe limits, while the low-pressure vent pipe manages gas during low-demand periods or system stabilization. Operators must adhere to strict safety protocols, including regular pressure checks, valve inspections, and leak testing, to mitigate risks associated with extreme temperatures and high-pressure differentials. Advanced control systems often integrate sensors and automated shutoff mechanisms to further enhance operational safety.
Applications and Maintenance Considerations
Cryogenic pump skids are widely used in industries requiring precise gas pressure management, such as LNG regasification terminals, chemical manufacturing, and renewable energy projects. Their modular design allows for easy integration into existing infrastructure, while their ability to handle extreme temperatures (-162°C for LNG) makes them indispensable in cryogenic environments.
To maximize longevity and performance, regular maintenance is essential. This includes inspecting seals and gaskets for cryogenic compatibility, lubricating pump components, and verifying the integrity of all piping and valves. Operators should also schedule routine performance tests to ensure the system maintains optimal pressure ratios and flow rates. By investing in proactive maintenance, facilities can minimize downtime, reduce energy waste, and extend the lifespan of their cryogenic pump skid infrastructure.
In conclusion, cryogenic pump skids are vital tools for converting stored cryogenic liquids into usable high-pressure gas. Their robust design, safety features, and versatility make them a cornerstone of modern gas processing and energy systems. By understanding their components, operational workflows, and maintenance needs, industries can leverage these systems to achieve greater efficiency, cost savings, and operational reliability in the face of demanding cryogenic challenges.