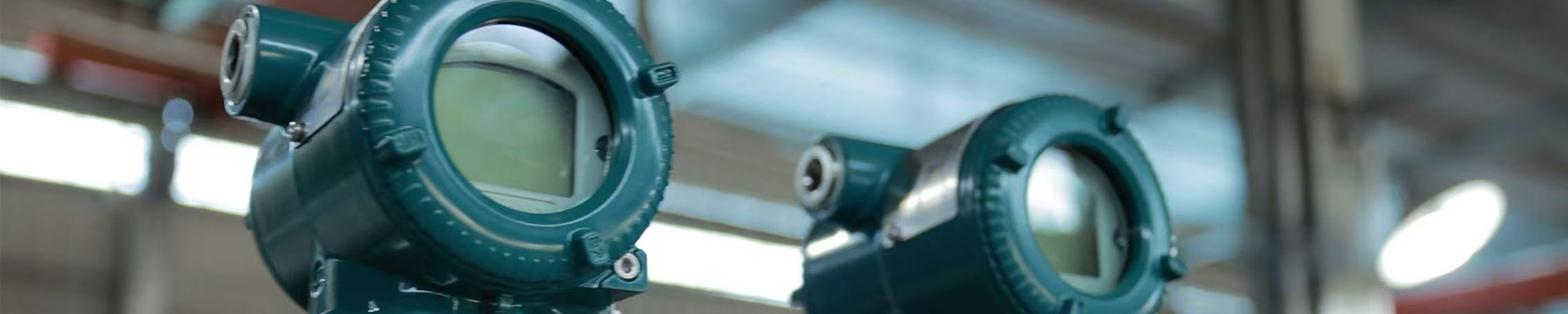
Step-by-Step Guide to LNG Fueling Operations
2025-03-26 22:15Step-by-Step Guide to LNG Fueling Operations: Safety Protocols and Pre-Cooling Procedures
Liquefied Natural Gas (LNG) has emerged as a clean, efficient, and versatile energy source for industries and transportation sectors. For LNG fueling stations, proper pre-cooling and systematic operational procedures are critical to ensure safety, efficiency, and compliance with international standards. This article outlines the detailed LNG refueling process, focusing on skid-mounted equipment setup, pre-cooling steps, and valve management protocols. Whether you’re a technician, plant operator, or fleet manager, understanding these steps will help optimize operations and minimize risks.
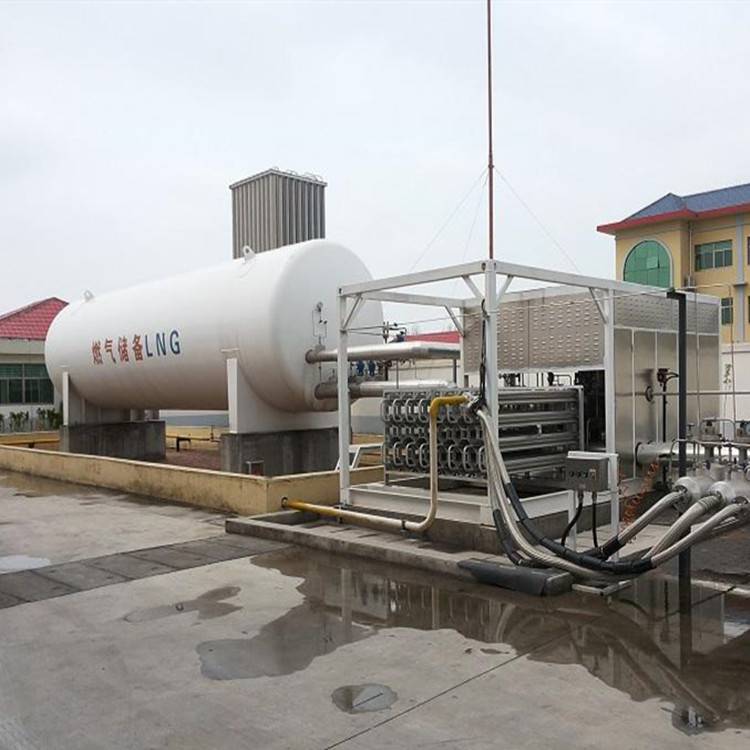
1. Pre-Operation Inspections: Safety First
Before initiating the LNG refueling process, operators must conduct a thorough inspection of the skid-mounted equipment and valves. Follow these steps:
Check Valve Status: Verify that all vent valves (high/low pressure), liquid-phase booster valves, gas-phase root valves, and emergency shut-off valves (ESVs) are in their correct positions. Ensure ESVs are closed during setup and that root valves for safety devices are open.
Instrument Air Pressure: Confirm that instrument air pressure is within the specified range to power control systems and pneumatic valves.
Emergency Systems: Test the functionality of emergency shutdown systems and ensure they are responsive to control signals.
This preparatory phase ensures the system is primed for safe operation and reduces the risk of leaks or pressure imbalances during subsequent steps.
2. Venting and Sealing: Establishing Safe Pathways
Once inspections are complete, proceed to activate the venting and liquid/gas pathways:
Open Gas Phase Valves: Gradually open the manual root valves for the storage tank’s gas phase, along with the pump pool’s gas-phase emergency shut-off valves.
Monitor Pressures: Check the pump pool pressure and inspect all flanges, seals, and connections for leaks. Address any detected leaks immediately to prevent system failure.
Proper venting prevents pressure buildup, while rigorous leak testing safeguards against environmental hazards and operational downtime.
3. Liquid Supply Activation: Opening Inlet Valves
With the venting system confirmed operational, initiate liquid flow from the storage tank:
Open Liquid Valves: Gradually open the manual root valves and emergency shut-off valves for the storage tank’s liquid phase. Simultaneously, activate the pump pool’s liquid-phase emergency shut-off valve.
Pre-Cooling Preparation: Prepare for the pre-cooling phase by monitoring temperature sensors and ensuring the pump pool is ready to handle cryogenic temperatures (-162°C for LNG).
This step transitions the system from inert gas venting to active liquid handling, requiring precise control to avoid thermal shock or valve malfunction.
4. Pump Pre-Cooling: Critical Temperature Management
Pre-cooling is a vital step to safely introduce LNG into the system. Follow these guidelines:
Initiate Pre-Cooling: Allow the pump to circulate LNG at low flow rates, gradually reducing temperatures to cryogenic levels.
Monitor Key Parameters: Track temperature changes in the pump pool and inspect valves, flanges, and seals for ice formation or leaks.
Safety Checks: Ensure the skid’s vacuum-insulated piping remains intact to minimize heat ingress. Verify that the station control system is in automatic mode, with all instrumentation displaying accurate readings.
Pre-cooling requires patience and continuous monitoring to prevent sudden thermal contractions that could damage components.
5. Final System Checks: Aligning Valves and Modes
Before commencing refueling operations:
Verify Valve Positions: Confirm that the storage tank’s liquid-phase inlet valves and emergency shut-off valves are open, while non-essential valves (e.g., pump unloading valves) remain closed.
Control System Mode: Switch the station control system to automatic mode and ensure all pneumatic ESVs are in their default (unactuated) positions.
Instrument Validation: Cross-check pressure, temperature, and flow rate parameters against predefined safety thresholds.
This final step ensures seamless integration between manual and automated systems, reducing the risk of human error during refueling.
6. LNG Refueling Operations: Starting the Process
Once pre-cooling is complete and all systems are verified:
Power Up the Refueler: Energize the LNG dispenser and initiate its pre-cooling cycle as outlined in the equipment manual.
Monitor Fluid Dynamics: Observe liquid circulation to ensure proper flow through the dispenser’s cooling loops. Address any irregularities, such as insufficient liquid return, which may indicate valve blockages or pump inefficiencies.
Commence Fueling: After successful pre-cooling and system validation, begin dispensing LNG to vehicles. Always adhere to safety guidelines for vehicle connection and fuel transfer.
7. Post-Operation Protocols: Maintenance and Documentation
After completing the refueling cycle:
Shut Down Safely: Gradually reduce flow rates and return the system to standby mode. Close all valves except those required for maintenance.
Leak Inspections: Conduct a final check for leaks or temperature anomalies in the skid-mounted components.
Record Keeping: Document all operational parameters, maintenance activities, and any incidents for future reference and compliance audits.
Why These Steps Matter
The LNG refueling process demands meticulous attention to detail, from valve sequencing to temperature control. Skipping pre-cooling or neglecting seal inspections can lead to catastrophic failures, including equipment damage or safety breaches. By following these steps, operators ensure:
Safety: Minimized risk of leaks, fires, or pressure-related accidents.
Efficiency: Optimal fuel flow and reduced downtime.
Compliance: Adherence to international standards like ISO 21899 for cryogenic systems.
For businesses seeking reliable LNG infrastructure, skid-mounted systems with automated controls and modular designs offer scalability and ease of integration. Partnering with certified manufacturers ensures equipment meets rigorous safety and performance criteria.
Conclusion
Mastering the LNG refueling process requires a balance of technical expertise and procedural discipline. By prioritizing pre-cooling, valve management, and systematic inspections, operators can enhance operational reliability while upholding the highest safety standards. Whether you’re establishing a new LNG fueling station or optimizing an existing one, understanding these steps is key to achieving long-term success in the rapidly growing LNG market.